Der integrierte Technologiedemonstrator wurde im Virtual Engineering Lab des Produktionstechnischen Zentrums Berlin eingerichtet und unter einem nutzerzentrierten Ansatz entwickelt. In dem Demonstrator wurden die verschiedenen Modelle und Methoden der Teilprojekte integriert und zusammengeführt. Ziel war es, sämtliche Aktivitäten und Prozesse abzubilden, die zur Herstellung eines Produkts erforderlich sind. Dies umfasst die Phasen der Produktentwicklung, Materialherstellung, Fertigung, Nutzung, Instandhaltung sowie die Rückführung im Rahmen nachhaltiger Kreislaufwirtschaftskonzepte.
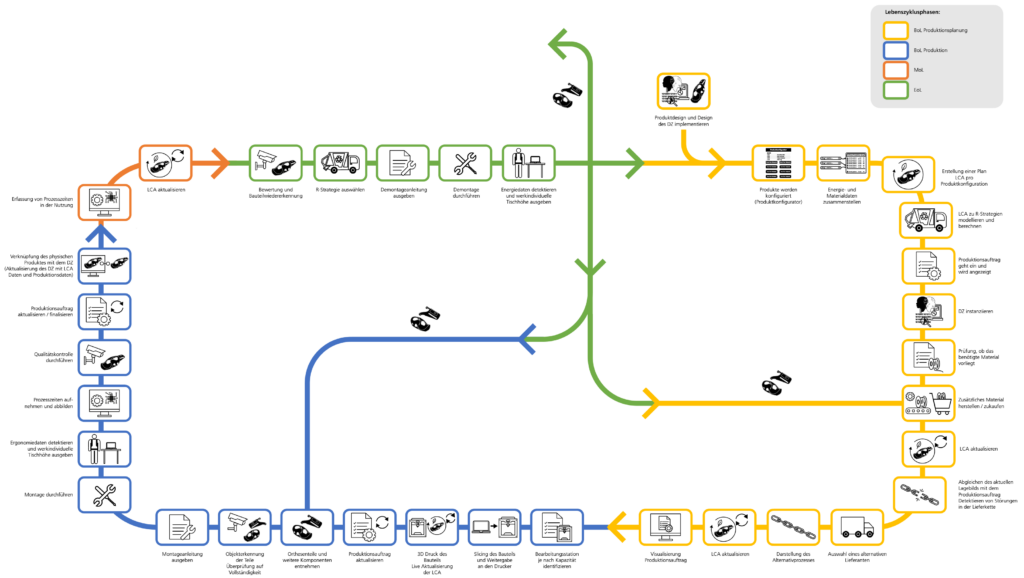
Im Teilprojekt „Geschäftsmodelle für die Biologische Transformation“ wurde ein Geschäftsmodell für die nachhaltige Produktion eines fiktiven Unternehmens entwickelt, das sich auf die additive Fertigung mit biobasierten Materialien konzentriert. Dieses Modell diente als Grundlage für den Demonstrator.
Das Teilprojekt „Bionische Integration für vernetzte Produktionssysteme“ fokussiert sich auf die Entwicklung eines interaktiven Lagebildes. Dabei handelt es sich um einen maschinellen Lernalgorithmus, der relevante Informationen für das Unternehmen und den Prozess identifiziert. Hierbei lag der Schwerpunkt auf der Identifikation eines Lieferantenausfalls aufgrund von Veränderungen im Unternehmensumfeld und der Suche nach alternativen Lieferanten.
Die einzelnen Prozessschritte und deren aktuelle Zustands- und Auftragsinformationen können durch die Multiagentensysteme verfolgt werden. Diese wurden im Teilprojekt „Ökologisch intelligente Services für die Produktion“ entwickelt.
Ein Multiagentensystem besteht aus mehreren Agenten, die miteinander interagieren, indem sie Informationen austauschen, kooperieren, Aufgaben verhandeln und koordinieren. Im Projekt BioFusion 4.0 werden Menschen, Maschinen und IT-Systeme durch Softwareagenten digital repräsentiert. Dadurch können sie miteinander kommunizieren und der Produktionsprozess kann selbstständig optimiert und geplant werden, bei gleichzeitiger Berücksichtigung von Störungen und Defekten.
Das Multiagentensystem besteht aus Mikrocontrollern mit kleinen Bildschirmen und Figuren, die in vordefinierten Führungsschienen liegen. Die Mikrocontroller repräsentieren die einzelnen Prozessschritte, während die Figuren die kundenindividuellen Aufträge darstellen. Durch das Verschieben der Figuren entlang der Führungsschienen zu den entsprechenden Arbeitsstationen werden die Prozessschritte gemäß den Vorgaben des Algorithmus abgearbeitet.
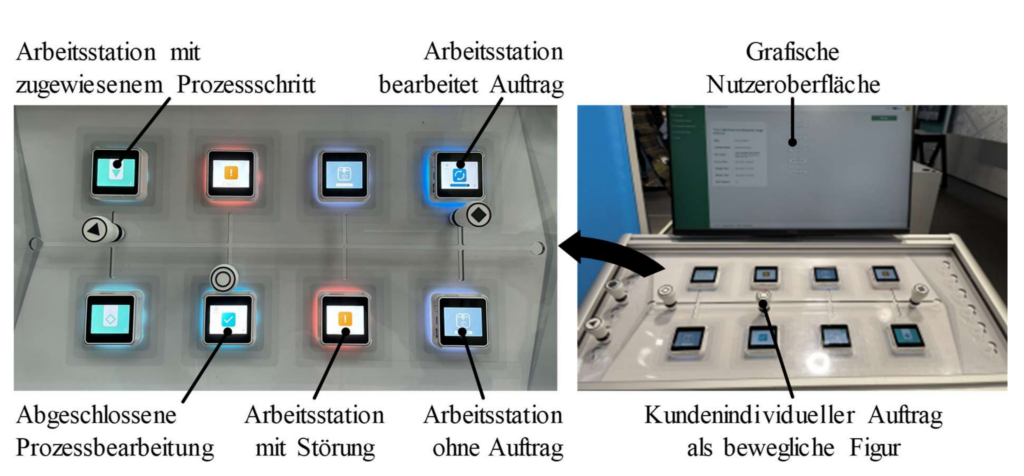
Nach der Vorbereitung, beispielsweise durch die Materialauswahl, wird das Produkt im 3D-Drucker gefertigt. Im Teilprojekt „Additive Fertigung mit biogenen und abbaubaren Polymeren“ wurde ein Verfahren entwickelt, mit dem verschiedene Bauteile aus biogenen und biologisch abbaubaren Polymeren hergestellt werden können. Im Demonstrator wurden Speiseabfälle als Substrat zur PHB-Produktion genutzt, um eine Daumenorthese mithilfe eines 3D-Druckers zu fertigen.
Anschließend ermöglichen die Ergebnisse des Teilprojekts „Intelligente Rückführung von Wertstoffen“ eine Objekterkennung, bei der spezifische Bauteile identifiziert und die Vollständigkeit des Produkts geprüft werden kann. Es wird automatisch eine Montage- bzw. Demontageanleitung ausgegeben und eine Qualitätskontrolle wird durchgeführt. Bei der späteren Demontage des Produktes, kann diese Technologie ebenfalls angewendet werden, um die Bauteile zu identifizieren und konkrete Verwertungsanweisungen auszugeben.
Ein weiterer Teil des Demonstrators ist die im Teilprojekt „Biointelligente Werker-Assistenzsysteme“ entwickelte Sensorweste, die die Arbeitenden ergonomisch unterstützen soll. Diese Weste ermöglicht eine Echtzeitanalyse der Körperhaltung und Bewegung und kann darauf basierend beispielsweise eine optimale Tischhöhe empfehlen, um unergonomische Haltungen zu vermeiden und die Gesundheit der Mitarbeitenden zu fördern.
Zum Demonstrator gehört auch ein Dashboard, auf dem ein lebenszyklusübergreifender Digitaler Zwilling des 3D-gedruckten Produkts dargestellt wird. Dieser wurde im Rahmen des Teilprojekts „Engineering biologisch transformierter Produkte“ entwickelt. Der Digitale Zwilling dient zur Analyse und Optimierung der ökologischen Nachhaltigkeit des Produkts. Anhand durchgeführter Life Cycle Assessments können im Demonstrator z. B. Materialien vollautomatisch auf ihre Nachhaltigkeit geprüft werden. Durch eine manuelle Auswahl eines Materials wird z. B. anschließend ein erster CO2-Fußabdruck bestimmt. Im Dashboard werden die verschiedenen Lebenszyklusentscheidungen und der individuelle ökologische Fußabdruck des Produkts visualisiert. Dabei gibt der Digitale Master den geplanten ökologischen Fußabdruck basierend auf den getroffenen Lebenszyklusentscheidungen an, während der Digitale Schatten Echtzeitdaten erfasst, aus denen der aktuelle ökologische Fußabdruck berechnet wird. Beide Werte werden im Dashboard dargestellt, sodass sie direkt nebeneinander betrachtet und verglichen werden können. Zusätzlich umfasst das Dashboard End-of-Life-Szenarien (Wiederverwendung, Rückgewinnung, Recycling, Entsorgung), um eine nachhaltige Wertschöpfungskette zu identifizieren.
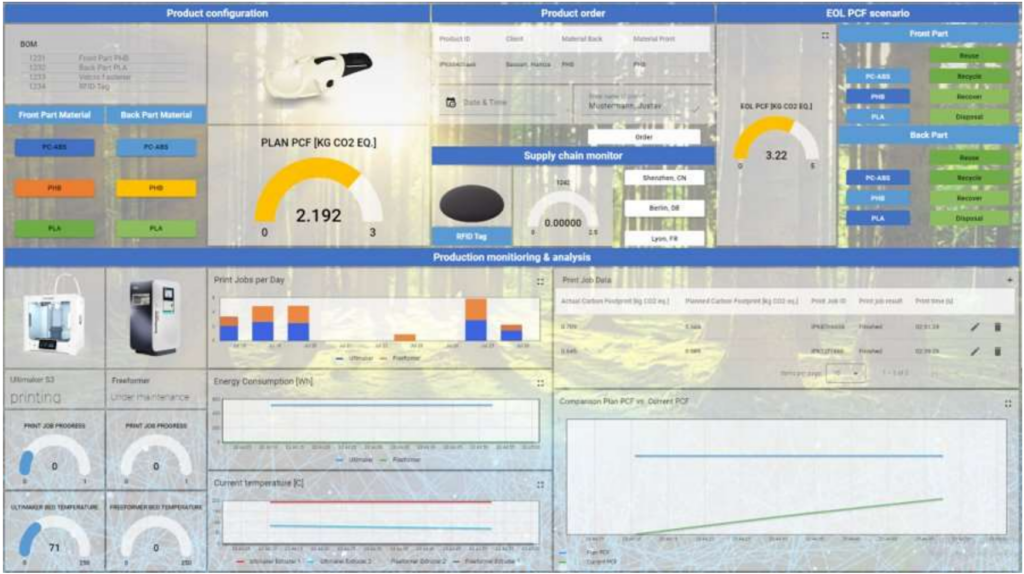